Revolutionize your power electronics designs with
The new benchmark for AC to DC power conversion
99.5%
FRONT-END EFFICIENCY
96–98%
POWER FACTOR
50%
LESS ENERGY WASTE
ZERO
INRUSH CURRENT
ZERO
INPUT VOLTAGE DERATING
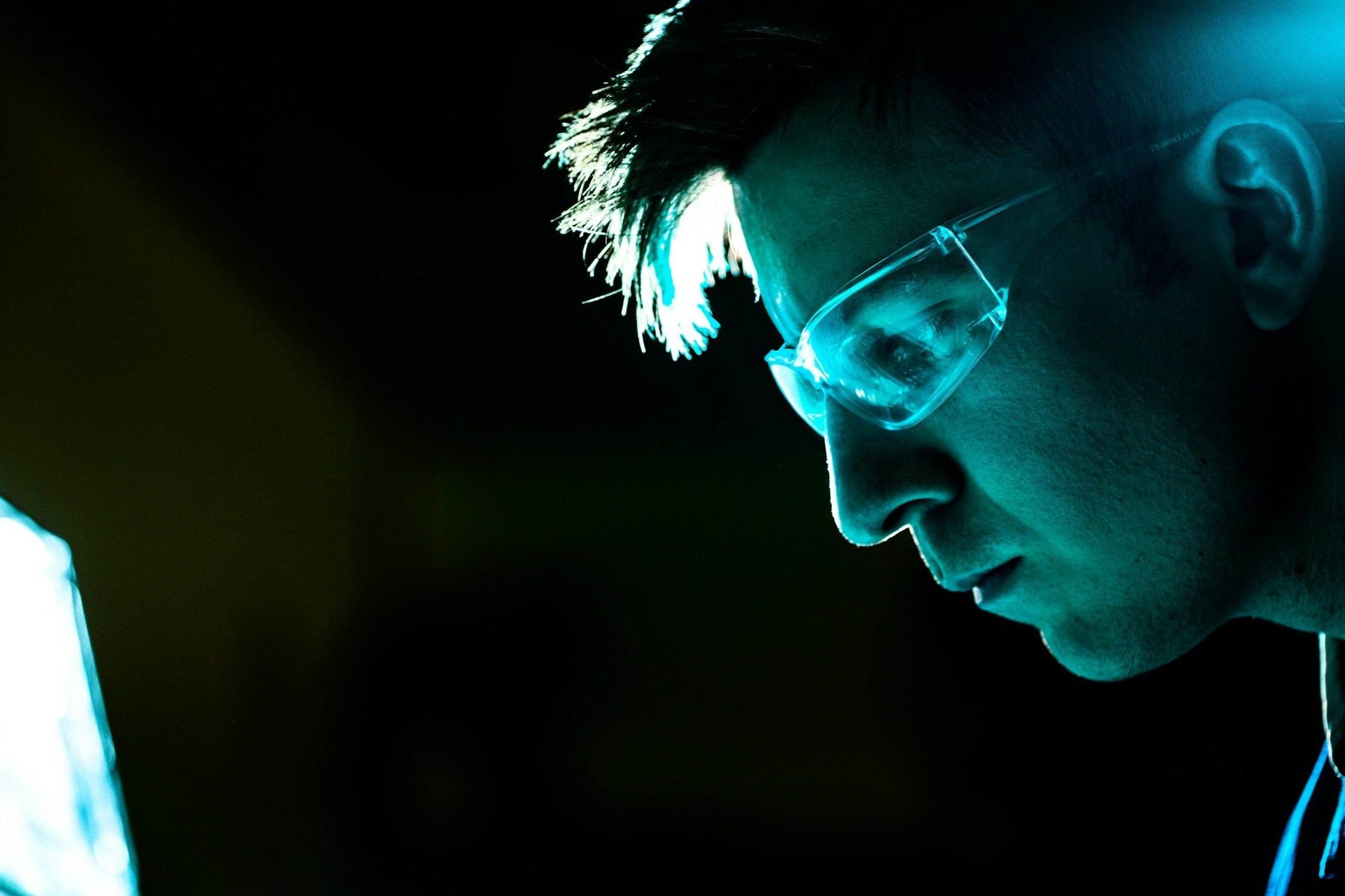
WHAT IS PULSIV
OSMIUM TECHNOLOGY?
Pulsiv OSMIUM technology is an AC to DC front-end conversion method that applies intelligence to an active valley fill approach and delivers a combination of game changing benefits in power electronics designs.
It significantly improves performance at low loads to increase overall average efficiency, reduce energy consumption and deliver a totally flat efficiency profile across all load conditions.
Pulsiv OSMIUM technology can be used with a variety of industry standard DC-DC converters including Flybacks, Forward Converters, & Asymmetric Half Bridge solutions. Where required, it also delivers Power Factor Correction as standard.
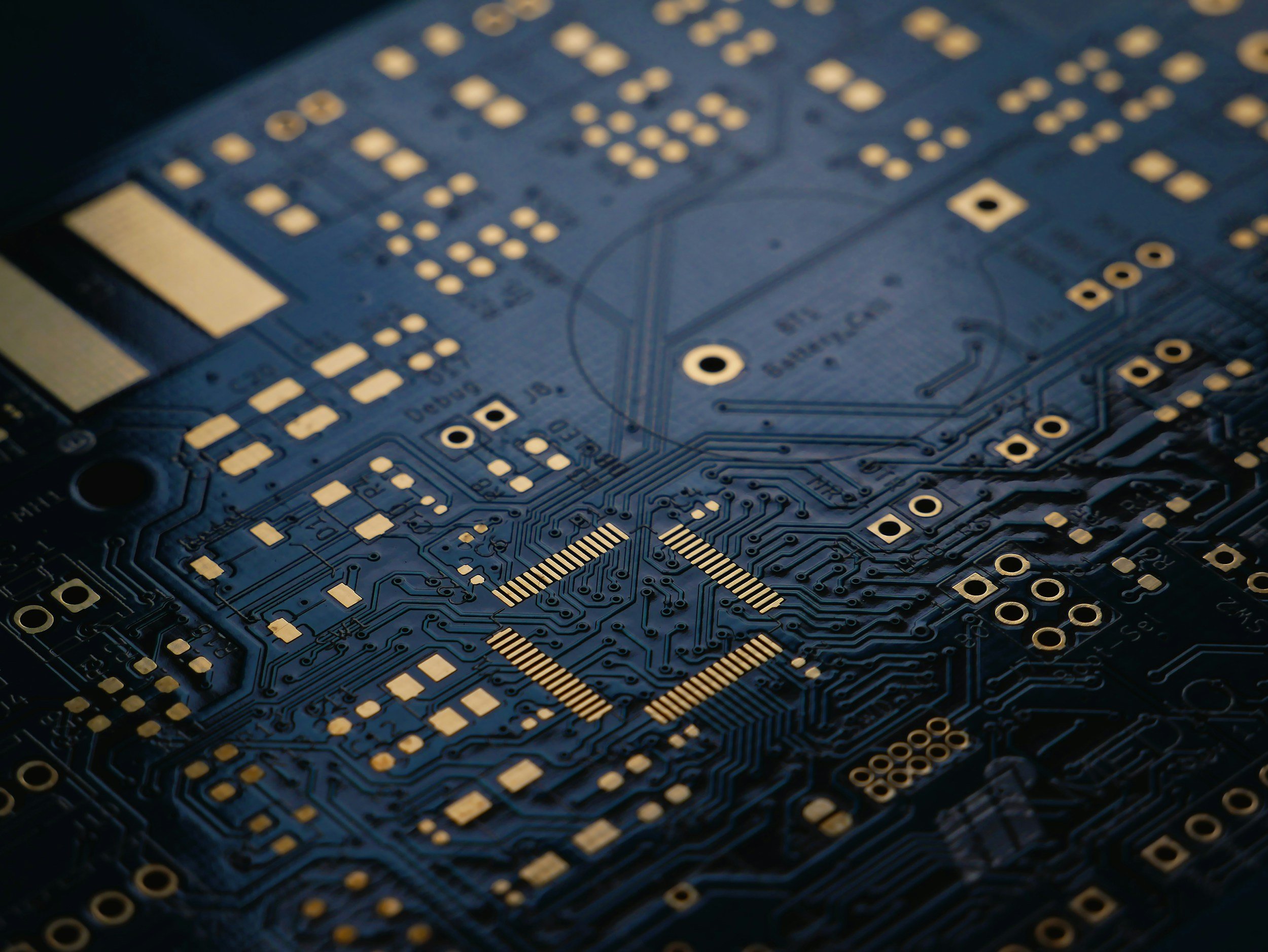
A UNIQUE COMBINATION OF BENEFITS
WORLD-LEADING FRONT END EFFICIENCY PROFILE
Pulsiv OSMIUM technology delivers exceptional performance gains at low loads. Our unique profile remains flat under all operating conditions to deliver efficiency levels of 99.5% peak and 97.5% average.
INCREASE OVERALL AVERAGE EFFICIENCY
As a result of improved performance at low loads, the average efficiency in a power electronics design can be increased by up to 50%. This directly impacts energy waste and overall power consumption under typical operating conditions.
ULTRA-COOL OPERATING TEMPERATURES
Pulsiv OSMIUM technology ensures critical system components operate at significantly lower temperatures when compared to conventional designs. This enables the use of smaller components, simplifies overall thermal management, and improves reliability.
INRUSH CURRENT ELIMINATED
We were the first company in the world to completely eliminate inrush current. This game changing achievement simplifies product design, reduces cost, and improves overall reliability.
INPUT VOLTAGE DERATING ELIMINATED
In a world’s first, Pulsiv OSMIUM technology has eliminated input voltage derating. We can deliver full power across the full universal input voltage range, without compromise.
COMPLY WITH THE LATEST REGULATIONS
Pulsiv OSMIUM technology minimizes conversion losses to reduce power consumption or increase the overall power budget. This flexibility enables products to maintain system functionality while complying with the latest regulations such as EcoDesign.

HOW DO WE COMPARE TO A BOOST PFC?
BOOST PFC METHODS
CONVERSION METHOD
Current is controlled with a boost inductor used in "series" to achieve a high power factor. 100% of the required energy must be stored at a typical voltage of 400V. All of the energy is switched through the boost PFC circuit which generates inevitable losses under low-load conditions and impacts the shape of the efficiency profile.
COMPROMISED LOW LOAD EFFICIENCY
In a boost PFC design, the series inductor used to achieve power factor correction is typically designed to deliver maximum performance at full load. Under lighter load conditions, this inductor will cause substantial losses and an efficiency roll-off. The compromised performance profile makes it more difficult to meet four-point average efficiency requirements demanded by EcoDesign regulations.
RESTRICTIVE HVDC
In a typical Boost PFC design, the required storage capacitance depends on the power required by the follow-on DC-DC converter and load fluctuations can dramatically impact capacitor voltage. As a result, the nominal HVDC is around 400V with a range of between 380V - 420VDC and capacitors must be rated accordingly.
COMPLEX POWER FACTOR CORRECTION
A Boost PFC controller regulates the current through the Boost inductor. The current is sinusoidal and the peak value of this current is determined by the power being used. This creates a critical dependency between the peak power and boost PFC operation. The peak current is managed on a cycle-by-cycle basis to keep the storage capacitor within a certain voltage range.
COMPLEX HALF-ACTIVE BRIDGE INTEGRATION
In a typical Boost PFC design, accurate zero-crossing detection is needed to implement a half-active bridge. Careful and complex circuitry design is required to support a universal mains input and there are recognised reliability implications.
INCREASED SWITCHING NOISE CAN AFFECT EMC COMPLIANCE
The current in a Boost PFC inductor is always switched in continuous conduction mode. The energy generated by switching currents will cause more noise and require additional filtering to comply with EMC regulations.
SLOWER TRANSIENT RESPONSE
In a typical Boost PFC design, the voltage on the output capacitor is regulated by the boost PFC. In order to maintain a high power factor, the controller must balance energy on a grid cycle by cycle basis.
MANAGING INRUSH CURRENT
In a Boost PFC design, a large inrush (typically from 30A - 80A) will always occur when first connected to the grid due to a conduction path through the boost diode and large capacitance. This is managed using inrush current limiting strategies which can include additional circuitry, and/or components.
BENEFITS
INNOVATIVE CONVERSION METHOD
A parallel capacitor is used to store only enough energy to ride through the AC valley period when the grid cannot support the load. Less than 50% of the required energy is stored in a capacitor typically rated at 200V. This significantly reduces losses at low-load conditions to deliver a flat efficiency profile.
BENEFITS
Increase efficiency at low loads
Improve system efficiency under all operating conditions
Lower operating temperatures
UNIQUE & FLAT EFFICIENCY PROFILE
In a Pulsiv OSMIUM design, the series inductor is replaced by a parallel capacitor to significantly reduce losses at lighter loads. As a result, a uniquely flat efficiency profile can be maintained across almost the entire load profile.
BENEFITS
Easier to meet global regulations
Increased power budget at low loads or in standby-mode
Overall average efficiency is improved
Energy waste is reduced
WIDER HVDC RANGE
In a Pulsiv OSMIUM design, a pre-determined storage capacitor voltage can be selected. The voltage range is 65-85VDC minimum (depending upon the DC-DC converter requirements) to the peak AC line voltage.
BENEFITS
Significantly lower parasitic capacitance losses at low power levels
Lower voltage rated capacitors save space, weight, and cost
In a Flyback design, smaller transformer cores can save space, weight, and cost due to lower primary side inductance
SIMPLIFIED POWER FACTOR CORRECTION
The Pulsiv OSMIUM microcontroller charges the storage capacitor to a pre-determined maximum value (set by the grid voltage) during every AC half cycle and the power required by the follow on DC-DC converter does not influence it's operation.
BENEFITS
Improved transient response for greater reliability
Maintains a high power factor of up to 0.98 over a wide input power range
Switch off or skipping power factor correction at low powers is not required
SIMPLIFIED HALF-ACTIVE BRIDGE INTEGRATION
When the storage capacitor is supplying the load, the line current is zero. This simplifies the switching of a half-active bridge which is controlled by Pulsiv OMSIUM as an optional feature.
BENEFITS
System efficiency is significantly improved at low-line AC voltages
Fewer components required saving space and cost
Overall system integration is simplified
Can improve reliability
LOW NOISE SWITCHING SIMPLIFIES EMC COMPLIANCE
In a Pulsiv OSMIUM design, the current required to charge a capacitor operates in discontinuous conduction mode. There is no energy associated with the inductor during switch on, so the overall noise generated in the system during the switching process can be dramatically reduced.
BENEFITS
Fewer and/or lower value filter components required
Improved conducted and radiated emissions
Overall EMC compliance is simplified
INSTANTANEOUS TRANSIENT RESPONSE
In a Pulsiv OSMIUM design, the charging of the capacitor is independent of the load behaviour. When the capacitor is supplying the load through the discharge diode, the system response is instantaneous.
BENEFITS
Improved stability during transient response
Ideal for loads requiring variable power requirements
Overall system reliability can be improved
INRUSH CURRENT ELIMINATED
The Pulsiv OSMIUM microcontroller manages the charging path of the capacitor. Since the switch is off during start-up and then carefully controlled, there is no parasitic path to the capacitor. Inrush current is therefore completely eliminated.
BENEFITS
Lower stress on the AC supply
Reduced system components
Improved system reliability
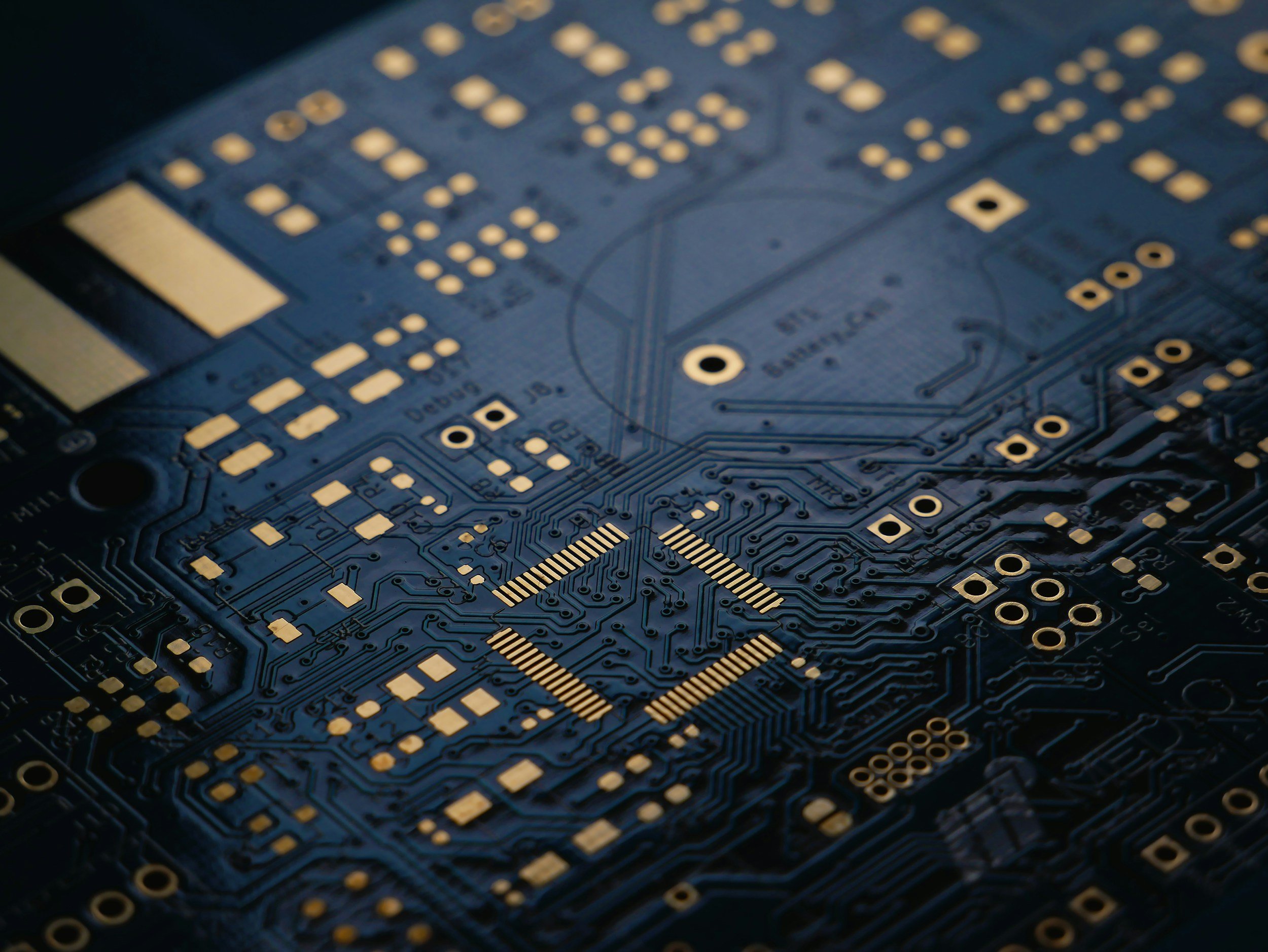
SIMPLIFYING THE DESIGN PROCESS
MICROCONTROLLERS
Our new method of efficiently converting AC to DC is achieved by using a Pulsiv OSMIUM microcontroller to monitor real-time grid condition, manage power factor correction (PFC) and regulate a high-voltage DC output to support a wide range of compatible DC-DC converters.
Our fully assembled, ultra-compact, and EMC compliant USB-C modules based on Pulsiv OSMIUM technology, can be customized to meet a variety of design requirements. NRE will be required (depending on complexity) plus MOQ’s, and are fully customized to a customer’s specification.
EVALUATION BOARDS: AC TO DC FRONT-END ONLY
Pulsiv OSMIUM AC to DC front-end evaluation boards allow you to quickly evaluate our power conversion technology for any application. They support universal input and can be adapted to test various front-end reference designs. Simply connect a suitable DC-DC converter on the HVDC output to produce a complete power supply prototype.
EVALUATION BOARDS: FULL AC TO DC POWER SUPPLIES
Our full AC-DC power supply evaluation boards include a Pulsiv OSMIUM front-end design and a carefully selected DC-DC converter to demonstrate a complete end-to-end solution. They have been developed for either general purpose or industry specific applications and require no additional modifications.
REFERENCE DESIGNS: AC TO DC FRONT-END ONLY
Our AC to DC front-end reference designs include a Pulsiv OSMIUM microcontroller and support a variety of different features and power levels. Once a configuration has been selected, simply integrate a suitable DC to DC converter to produce a complete power supply design.
REFERENCE DESIGNS: FULL AC TO DC POWER SUPPLIES
Our full AC to DC reference designs deliver a complete end-to-end solution that combine a Pulsiv OSMIUM microcontroller, AC to DC front-end reference design and a carefully selected DC-DC converter. Developed for both general purpose and specific applications, they can be adopted without making any changes or further modified according to the needs of the end product.
STANDARD ASSEMBLED MODULES: USB-C
Our fully assembled, ultra-compact, and EMC compliant modules based on Pulsiv OSMIUM technology using our full AC to DC power supply reference designs. Developed for rapid prototyping and to demonstrate a size optimised “Plug & Play” solution, they can be easily integrated into end products without incurring any further design, development, or manufacturing costs.